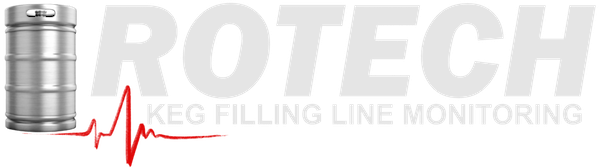
About Rotech
Racker monitoring has been a Rotech core business speciality since 1988, and the Rotech System is the world leader in electronic keg systems — copied, but unequalled.
Totally Independent
We do not supply any other line equipment or rackers.
We have installations with most major brewing Groups worldwide (including Carlton & United, MolsonCoors, SAB-Miller, Heineken, AB-InBev, Carlsberg, Lion Nathan, Fosters, Sapporo, Diageo/Guinness), and a host of smaller groups and independents.
Data Archives
We have thousands of archive records from every type and size of filler worldwide — from the smallest single lane to the largest multi-line 3-carousel rotary; and from every type and size of keg from 5-litre to 163-litre (36 Imp. Gal).
Signifiicantly Improve Operations
Cost Reductions and Quality Improvements
Full Analysis Service
Rotech products and services
The Rotech Keg Line Monitoring System: – everything you need (hardware and software) to monitor and take control of your filling line
- Includes Keg and Tablet, Bluetooth ready
- Calibration service – independent service for repair and recalibration
- Training and visits
- Trace analysis, Advisory and consultancy – unique confidential service to supplement and help the brewery’s own analysis
- Purchase includes – two year package or lease
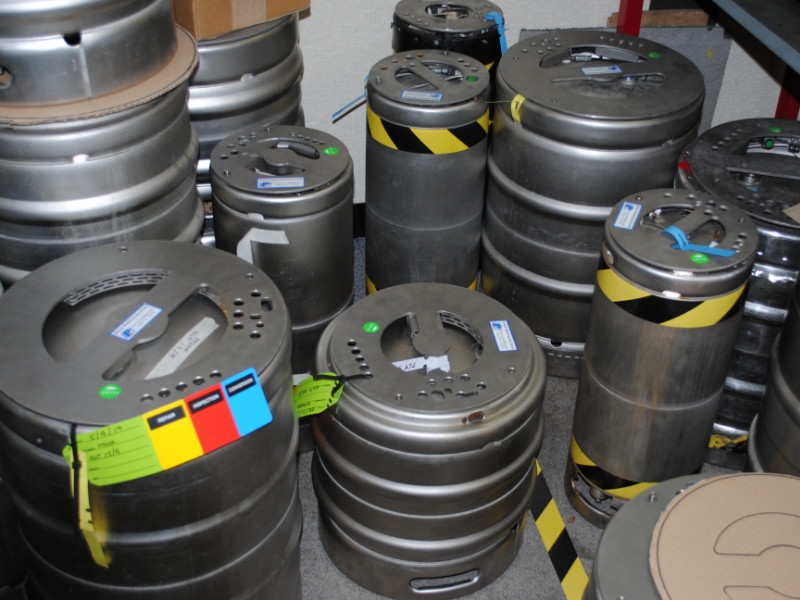
Ensuring filling lines are optimised
The effect of what we do is to ensure that each brewery, using our technology, is able to guarantee that the process that cleans their kegs has removed contaminants, yeasts and residues that taint beer.
In addition, the use of the Rotech keg enables each brewery to tune their line. This unique technology may enable to save up to 10% savings in utilities, chemical and reduce beer losses. This makes the investment in an Electronic Keg supplied by Rotech a “no brainer”.
New Technologies
- Bluetooth Now standard
- Advanced software , User Interface development
- Platform development
- Windows Tablet and Phone
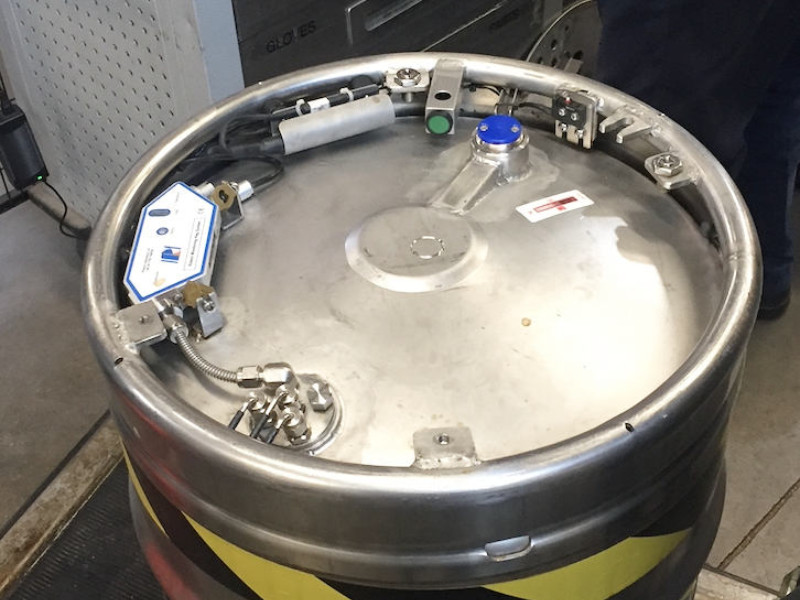
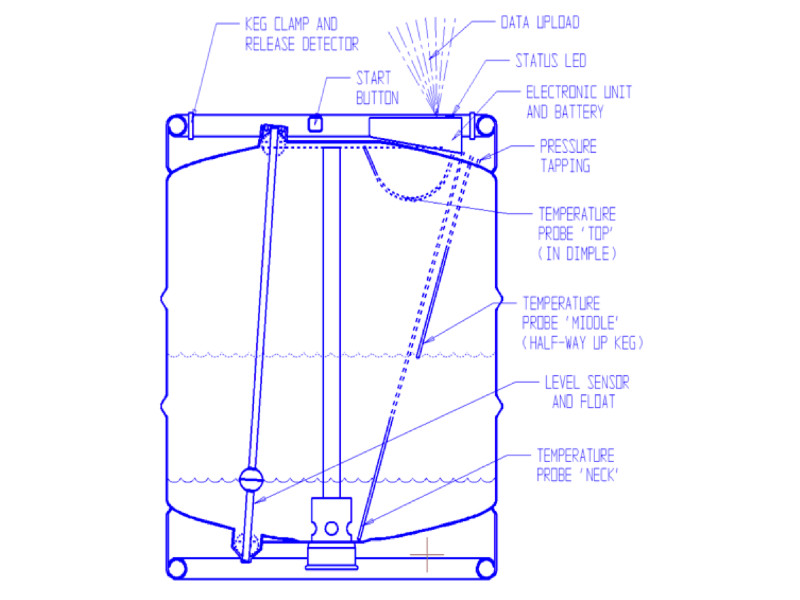
Sensors in the Rotech Keg
Here are some of the conditions the Rotech Keg will show:
- Poor/weak washing (low pump pressure)
- Pools in the keg during washing (poor practice)
- Liquid carry-over from head to head (intentional or not)
- Spear tube washing (‘trickle-back’)
- Air in the keg during steam disinfection (hygiene risk)
- Too low/too high steam temperatures
- Disinfection steam quality/saturation
- Temperature distribution in the keg (often not uniform)
- Hygiene risks at any time
- Risks/causes of high DO’s in the beer
- Risks/causes of high micros (regular or occasional)
- Rate of filling/emptying (water, detergents, beer)
- Fill performance
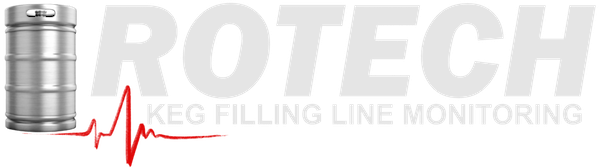